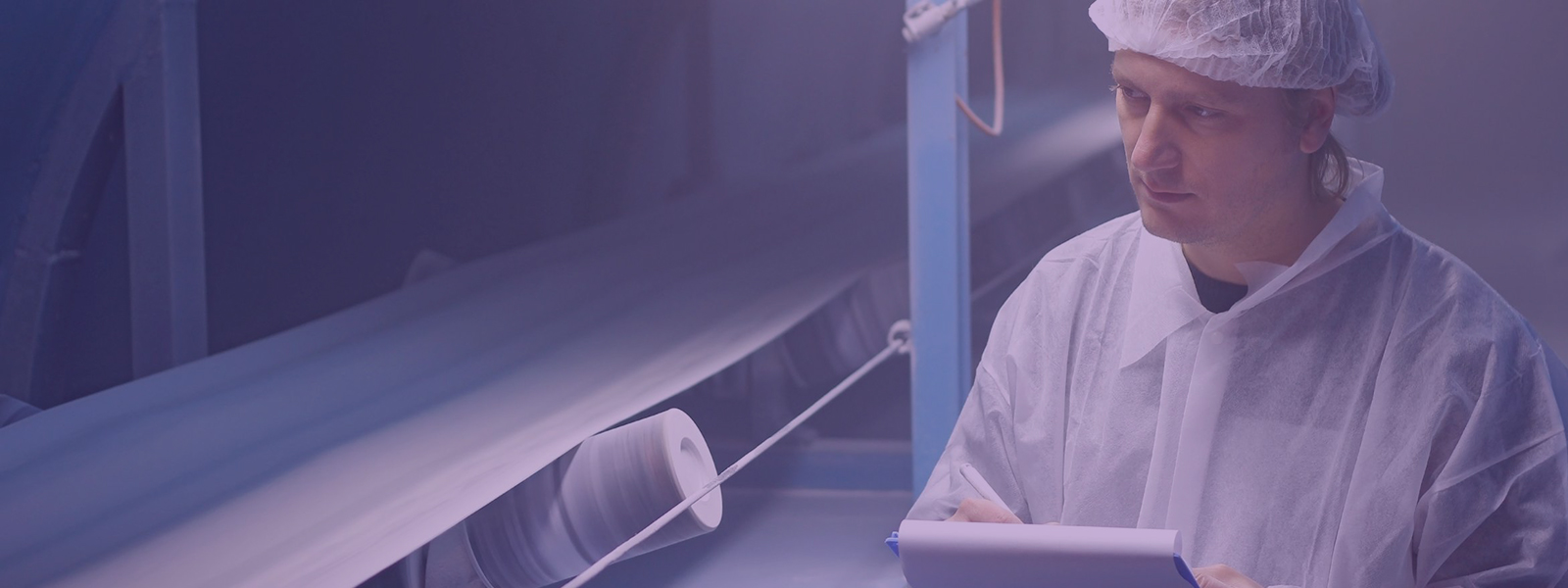
Industrial Sector
Energy consumption in the meat sector
Meat processing requires large areas of the cooling plant for space cooling and refrigeration, which can mean high energy costs. Energy costs for meat plants represent the fourth highest operational cost – after the costs of raw materials, labour and waste disposal, and the survival of your business depends on keeping costs to a minimum.
Our energy auditing work in the meat sector has shown that managing energy use is still in its infancy. But energy usage and costs are not uncontrollable costs. Energy usage and cost can be reduced by as much as 45% in the meat sector using an array of technologies and analyses.
Our work has also shown that typically 50% – 80% of the energy used in an abattoir plant is provided by electricity from the grid and the other 20% – 50% coming from thermal energy generated on site by oil, gas or coal.
The specific energy consumption of various types of meat – depending on the carcass treatment process – is shown in the table below. Contact us for more information on energy efficiency in your sector.
Comparison of Specific Energy Consumption (SEC) ref values (in primary energy): the effect of freezing, cutting and deboning meat
Energy saving opportunities in the meat industry
The top energy saving opportunities for a meat plant operation are shown here.
- The installation of an energy sub-metering system
- The installation of a biogas recovery system
- The installation natural gas-fired cogeneration or a tri-generation systems
- Chilled water spray or evaporative pre-cooling of carcasses
- Refrigeration plant improvements
- Waste heat recovery from cookers, flash steam, and better condensate recovery
- Boiler plant optimisation, including a boiler tune-up, and use of economisers
Our Energy Efficiency Services
Below are the energy efficiency services we provide. Contact us for more information on these services.
Comprehensive energy audit
Maximpact’s energy audit will cover all thermal and electrical process plant and utility systems. Our comprehensive energy audit specification will provide you with a detailed specification of our services and saving potential which is typically between 20% and 40% of your existing energy bills.
New equipment energy efficiency specification
Are you considering purchasing a new two-stage refrigeration plant or a new steam boiler?
If so, we can ensure that your vendors provide efficient equipment that will help save on the cost of running it over its lifetime. We can help you include energy efficiency specifications in your tender documents that will ensure all bidders bid on a level playing field.
Perform an energy management system gap analysis
We will study your existing energy management practices and determine what steps are required in order for you to implement an energy management system such as that provided by the international energy standard ISO 50001, often called a gap analysis study.
Training in energy awareness
Maximpact can provide employee training in energy awareness associated with good plant operational practices.
ISO 50001 full implementation support
We provide support for full implementation of the global energy management system standard ISO 50001 in your factory. ISO 50001 specifies requirements for establishing, implementing, maintaining, and improving an energy management standard.
Plant resilience audit and recommendations action plan
How prepared are your manufacturing processes to cope with weather extremes caused by global warming?
Can your manufacturing and utility systems cope with climate extremes such as the polar vortex extending over northern parts of the United States in December 2022 that came with temperatures as low as -50⁰C?
The purpose of our resilience study is to determine how exposed your manufacturing and utility systems are to the extremes in weather that will be more often experienced throughout the world due to climate change.
These extremes are occurring right now. It was common practice in the past to design processes for specific minimum low, ambient low, and high temperatures based on weather statistics averaged or typically 50 to 100 years. Global warming has changed these statistics, but many design engineers have not yet changed their practices.
We have formulated an approach to assess your process and utility systems and their resilience to climate change. Don’t wait until your process vulnerabilities are revealed by extreme weather events, and you must pay high costs for lost production and product output. Act now and be prepared.
Renewable Energy for the Meat Sector
- A feasibility study of the installation of solar water heating for domestic hot water use.
- A feasibility study of the installation of solar photovoltaic systems to displace imported grid power.
- A feasibility study for utilising a renewable energy boiler to produce hot water for sterilisation of knives and other deboning equipment. The new boiler could use biofuels such as wood pellets or other renewable energy sources.
- A feasibility study of installing a co-generation or tri-generation systems to supply electricity, hot water heating for sterilisation and water at 10⁰C suitable for cooling the meat factory boning halls.
- A feasibility study of using waste from the factory to produce methane gas in an anaerobic digester unit and supply this methane to run a co-generation or tri-generation system. Such as system could displace grid power and supply hot water, steam and cooling water to the factory processes.
Sectors of Focus
AGRICULTURE | ASSESSMENT | BIOMIMICRY | CLEAN TECHNOLOGY | COMMUNITY | CONSTRUCTION | CSR | ECO-TOURISM | ENVIRONMENT | FINANCE | FORESTRY | GREEN BUSINESS | MARINE | NOT-FOR-PROFIT | POLLUTION | STRATEGIC DEVELOPMENT | RENEWABLE ENERGY | WASTE MANAGEMENT | WATER | WOMEN’S EMPOWERMENT
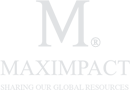